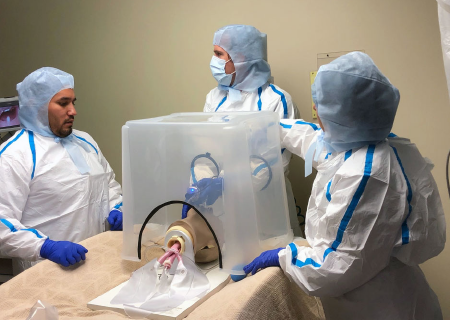
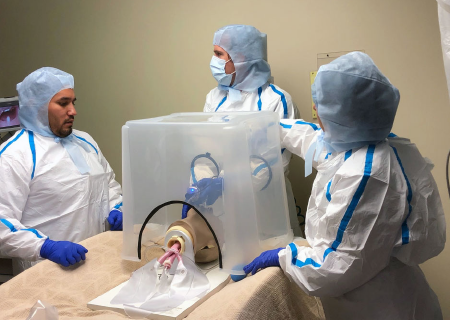
Thanks to a wave of community donations, the technical know-how of a local artist and the medical acumen of a regional medical giant, a new type of protective device for health-care workers has been created to help front-line staff stay safe while treating patients with COVID-19.
Known as “intubation boxes,” the clear, plexiglas containers limit medical workers’ exposure to airborne droplets during procedures known as intubation or extubation, when a tube is either inserted into, or extracted from, a patient’s body for ventilation or other procedures.
“When intubating or extubating, particles exist in the air as a result of the procedure,” said Dr. Adam Glasofer, chief innovation officer of the Virtua Center for Innovation. “If a patient is infected, there are going to be infectious particles around. COVID-19 is a virus and it acts the same way (during the insertion or removal of the tube),
“By placing the enclosure over the patient, we are stopping the spread of the particles and shielding the doctors,” the doctor added. “Prior to this, we hadn’t seen something quite so virulent that required such intense protection.”
Dr. Glasofer served as an unofficial advisor for the initiative, spearheaded by Pearlman Designs in Voorhees and Ascalon Studios in West Berlin. Working together, the two family-owned companies have fashioned more than 100 intubation boxes.
For David Ascalon, a Cherry Hill resident who owns the studio — which specializes in stained glass and sculpture — the project provided an opportunity to apply his talents in new ways.
“If you work with your hands and know the tricks of the trade, you can do anything,” Ascalon said. “It’s gratifying to help the people who help save lives.”
Joining Ascalon in his studio space was his 17-year-old grandson, Zaiden, along with Bob Loch and Seth Pearlman.
“Given the Governor closed up businesses early on in March, we found we had the space to do the work,” Ascalon explained. “We received a number of materials and donations from people and private companies, and we assembled everything in my studio. We had the capability and when Seth approached us to do it, and with nothing else going on, we got right to fabricating them.”
As Ascalon further revealed, conceptualization for the device was actually performed long before the process began locally, thanks to an idea from a doctor in Thailand
“We can’t take credit for the process, but for us, the physical crafting of the boxes was a way of taking up the cause with something we were capable of doing here,” Ascalon added.
“We had what’s called an acrylic bender, which was a donation by a major equipment seller, and we were able to put it right to work after getting all the parts in order for the fabrication.”
The turnaround time for a device to be completed, according to Ascalon, ranged from a single overnight shift and no more than a couple of nights.
“Glasofer approached us to find out about the boxes,” Ascalon said. “He asked for a sample, tried it out and was pleased with the results, and we then sent another five to Virtua Hospitals in the area.
“And as we speak, they are being used,” he added. “At this moment, we have had very little call for them since, and that’s a good sign because it means there is less of a need.”
Ascalon had 14 more boxes at his disposal, available free of charge.
“We supply the transportation for the boxes, as long as it’s local,” he noted. “We’ve actually had one request for a box up in Boston, and we had one of our drivers take it up there.
“It’s our duty to do what we can for the cause.”
Glasofer and his fellow Virtua clinicians tested and refined the initial prototype and made recommendations that helped determine the final design. Today, 10 such boxes are now in use among Virtua’s five hospitals.
“ICU teams are finding great value in the boxes. They provide a sense of comfortability during procedures,” Glasofer added. “For an unbiased, outsider perspective, it’s important to look to professionals beyond the health-care industry for viable solutions.”